Operational Techniques Assignment Help Difference between JIT Demand Based System and Forecast Driven Systems To increases operational effectiveness, it becomes essential to know about difference between different operational management systems. It is because it helps the firm to adopt more effective and appropriate operation management technique. Concern of this, JIT demand based system and forecast driven system are different from each other in terms of application, pros & cons, time, etc. In the case of JIT demand based system, it is found that this system is related with the intended omission of waste and constant improvement in the productivity (Zhang, Wang & Wu, 2012). This system is mainly concerned to do right thing at the right place at the right time to improve organizational performance and productivity.
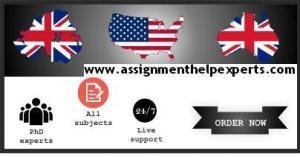
Positive result of using this system at the workplace is related with the limited requirements to fulfill the commitment as only labor and resources are required to accomplish the tasks and to meet with needs of the customers. But, requirement of much time to distribute the firm’s products is the negative point of using this system that may affect sales and profitability of the firm. It is because it may diminish services of the firm in the case of sudden increase in demand of the customers (Dudbridge, 2011). At the same time assignment help experts said that, it is found that forecast driven system may risky for the manufacturing firms as it is based on anticipated sales, expenses and profits and these may be changed as per the changes in market condition and parameters. But the positive direction of using this system is related with the effective inventory management as this system assists the company to keep inventory on hand and providing effective and efficient customer services (Zhang, Wang & Wu, 2012). It is because availability of the products or inventory management of the firm helps the firm to provide products as they are demanded by the customers. The negative point of using this management tool is related with less accuracy in forecasting. Unlike JIT, in case of decline in anticipated sales, excess inventory could result into waste that is negative point, which may affect the firm financially (Danese, Romano & Bortolotti, 2012). So, it can be stated that JIT and forecast driven systems are different from each other in terms of uses and benefits for organizational growth and success. You can also get case study help on forecast techniques.
Pros and Cons of JIT and Lean Manufacturing Systems There are various pros and cons of JIT and lean manufacturing system that helps to determine use of these systems at the workplace. Lean manufacturing supports to the continuous improvement in productivity through using resources effectively, reducing cost and maintaining quality of the organization’s operations, while maintaining higher standard of the production from top to bottom (Furlan, Vinelli & Pont, 2011). Additionally, another benefit provided by lean manufacturing is that it maintains level of operation in terms of working on every process every day consistently in same manner (Dudbridge, 2011). It also helps the firm to minimize unnecessary movement of workers, machines, goods and needs for storage space that is beneficial for the firm in terms of reducing extra expenses. Minimization in defects and elimination of wastage of material is other benefit of lean manufacturing system (Wu, 2003). At the same time, this system is not beneficial for small and medium sized firms as it takes huge time and cost that is not beneficial for these types of companies that is countered as disadvantage of this system (Allen, Maguire & McKelvey, 2011). On the other hand, JIT system is beneficial for the firms as it uses cash flow in effective way in terms of estimating expenses of the firm. This system also responds to the customers’ demand that helps the firm to manage inventory and improve overall production by enhancing customer satisfaction (Danese, Romano & Bortolotti, 2012). JIT affect the supply chain of the firm in case of inability of suppliers as supply and production depends on the effectiveness of JIT (Guerra & Cianchette, 2006). Both systems JIT and lean manufacturing reduce the wastage and non-valuable activities through adopting the process that can eliminate the wastage from the operational part. Effective material handling system, solid preventive maintenance system and increase in employee responsibility are the important elements of JIT and lean manufacturing systems that ensures to reduce non-value added or wasted activities in the operations (Danese, Romano & Bortolotti, 2012). Avoidance of unnecessary activities such as overproduction, wasting time, defective products, waste of inventory and waste of transportation expenses is also a common goal of both systems. These activities help to spread ethical working environment and support the management to follow TQM (total quality management) techniques at the workplace to reduce the wastage and non-value activities (Furlan, Vinelli & Pont, 2011).
Challenges of JIT System Although JIT system is beneficial for the organizational growth, but some challenges are also associated with it that makes it difficult for the firms to use this system as it requires lot of time for planning to implement. Firstly, requirement of skilled and knowledgeable employees, who have knowledge about the JIT system and its uses at workplace, is the major challenge for the firm (Furlan, Vinelli & Pont, 2011). It is because to follow this system, implementation team is required that demands knowledgeable employees in the area of JIT. Another challenge is related with the time and efforts that need to understand the user’s context and make the JIT system meaningful (Guerra & Cianchette, 2006). The firm also requires building a good relationship with suppliers and significant distribution system for the implementation of JIT. References Allen, P., Maguire, S & McKelvey, B. (2011).The Sage Handbook of Complexity and Management. USA: SAGE Publications Ltd. Danese, P., Romano, P & Bortolotti, T. (2012). JIT production, JIT supply and performance: investigating the moderating effects. Industrial Management & Data Systems, 112(3), 441 – 465. Dudbridge, M. (2011). Handbook of Lean Manufacturing in the Food Industry. USA: John Wiley & Sons. Furlan, A., Vinelli, A & Pont, G. D. (2011). Complementarity and lean manufacturing bundles: an empirical analysis. International Journal of Operations & Production Management, 31(8), 835 – 850. Guerra, J. A & Cianchette, C. (2006). Just-in-time Information: a layered approach to information design. Retrieved April 23, 2012 from http://slant.avenuea-razorfish.com/1206_slant/jit.pdf Wu, Y. C. (2003). Lean manufacturing: a perspective of lean suppliers. International Journal of Operations & Production Management, 23(11),1349 – 1376. Zhang, Y., Wang, Y & Wu, L. (2012). Research on Demand-driven Leagile Supply Chain Operation Model: A Simulation Based on Any Logic in System Engineering. Systems Engineering Procedia, 3, 249-258. You can get 24X7 assignment help of all subjects. We assure you that you will get complete and original assignment help within the deadline.